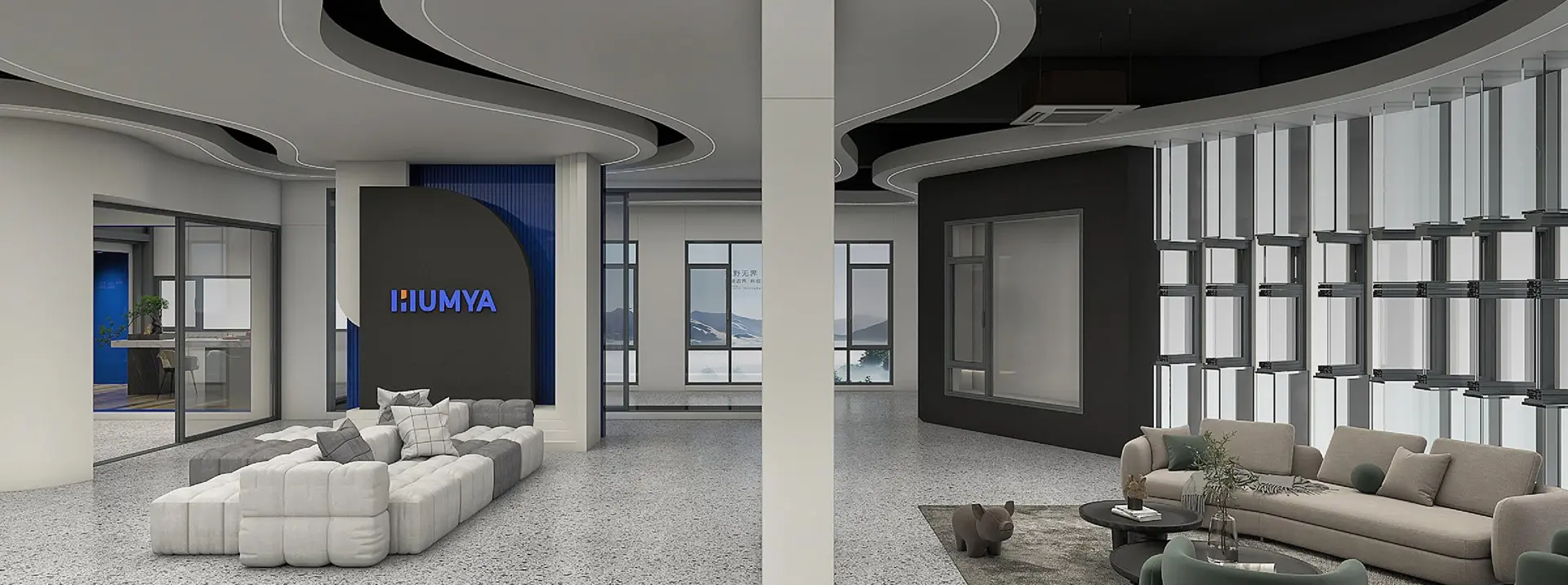
Understanding the Quality Benchmarks of Sliding Back Doors in Modern Manufacturing
In modern manufacturing, the design and functionality of components play a critical role in ensuring efficiency and safety. Among these components, the Sliding Back Door stands out as a vital element used in various applications, from transportation to industrial facilities. Understanding the quality benchmarks associated with Sliding Back Doors is essential for manufacturers aiming to deliver reliable and durable products. These benchmarks encompass factors such as material strength, design integrity, and operational efficiency, all of which contribute significantly to the overall performance of sliding doors in real-world scenarios. As the industry continues to evolve, it becomes increasingly important for manufacturers to adhere to established quality standards while also adapting to technological advancements. This blog will delve into the key quality benchmarks of Sliding Back Doors in modern manufacturing, exploring how they influence both production processes and end-user satisfaction.
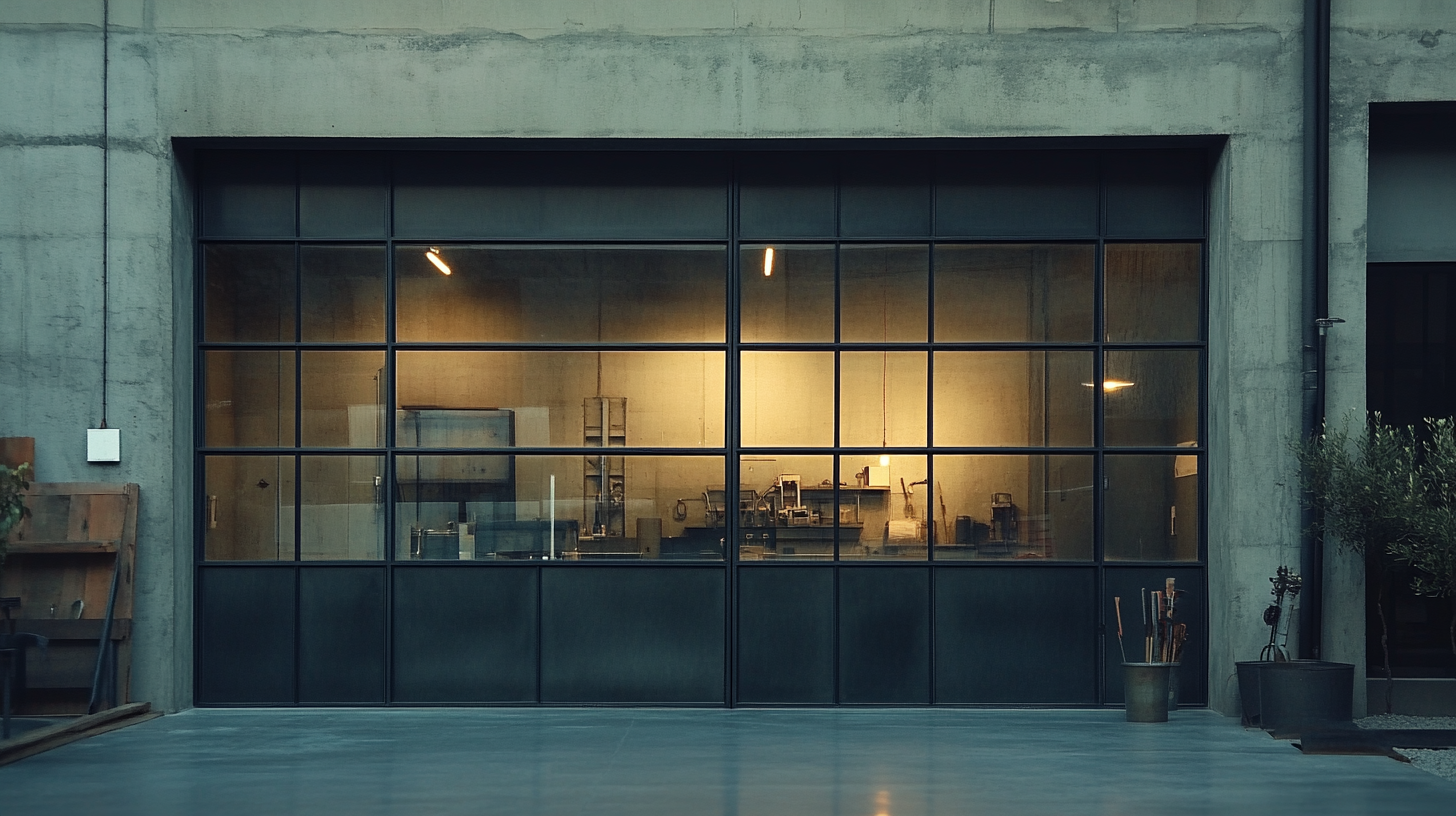
The Importance of Quality Benchmarks in Sliding Back Door Production
Quality benchmarks play a crucial role in the production of sliding back doors, ensuring that manufacturers meet both safety and performance standards. In an industry where precision is key, these benchmarks serve as a baseline for measuring the durability, functionality, and aesthetic appeal of the final product. By adhering to established quality metrics, manufacturers can enhance the reliability of their sliding back doors, ultimately leading to higher customer satisfaction and fewer costly recalls.
Moreover, the importance of quality benchmarks extends beyond mere compliance; they foster continuous improvement in the manufacturing process. By regularly reviewing and updating these standards, manufacturers can stay ahead of industry trends and innovations. This proactive approach not only helps in minimizing defects but also promotes efficient use of resources, thus optimizing production timelines and costs. Ultimately, implementing rigorous quality benchmarks is essential for modern manufacturing as it ensures that sliding back doors not only meet consumer expectations but also uphold the brand’s reputation for excellence.
Key Materials and Design Considerations for Enhanced Durability
In modern manufacturing, particularly in sliding back doors, the choice of materials and design considerations plays a crucial role in enhancing durability. Recent advancements in sustainable materials, such as the integration of fiber reinforced ultra-high performance concrete (UHPC), showcase promising developments. According to industry reports, UHPC's incorporation of nanomaterials and fibers not only boosts performance but also contributes to sustainability efforts within the construction sector. This is evident as more manufacturers seek eco-friendly alternatives without compromising on strength or durability.
When selecting materials for sliding back doors, it's essential to consider both physical properties and longevity. High-strength steels, for instance, are now being formulated to combat hydrogen embrittlement, a significant concern in high-performance applications. Recent studies highlight that chemical heterogeneity within these steels can improve their resistance, achieving a balance between strength and durability. Incorporating materials that resonate with sustainability goals can also enhance market appeal and compliance with modern regulations.
**Tips:** Always analyze the specific environmental conditions your sliding back door will be subjected to, and choose materials that offer resistance to those conditions. Additionally, consider utilizing biodegradable polymers for less load-bearing elements, as they align with sustainability goals while maintaining functionality. Regularly evaluate and optimize the design for durability and maintenance efficiency to ensure long-term performance.
Understanding the Quality Benchmarks of Sliding Back Doors in Modern Manufacturing - Key Materials and Design Considerations for Enhanced Durability
Material | Durability Rating | Weight (lbs) | Cost per Unit ($) | Design Considerations |
---|---|---|---|---|
Aluminum Alloy | High | 20 | 150 | Corrosion-resistant, lightweight |
Steel | Very High | 35 | 200 | Strong, requires protective coating |
Fiberglass | Moderate | 15 | 100 | Good thermal insulation, flexible design |
Composite Materials | High | 18 | 180 | Lightweight, enhanced structural properties |
Methods to Assess the Performance of Sliding Back Doors
In modern manufacturing, the quality benchmarks for sliding back doors play a critical role in ensuring safety and efficiency in logistics. As transportation practices evolve, it is essential for manufacturer and operators to regularly assess the performance of sliding back doors using robust evaluation methods. Industry standards suggest that the operational strength of sliding doors should be rated for at least 10,000 open-close cycles while maintaining a minimum load restraint capacity of 2,000 kg. This ensures that the doors can withstand the rigorous demands of loading and unloading processes without compromising safety.
Recent guidelines on safe handling during load securing highlight the significance of proper design and performance assessment of side gates and curtains. Effective lashing techniques and the use of tensioners are crucial in preventing load shifting, which can lead to accidents. Reports indicate that around 30% of transport-related incidents are linked to inadequate load securement, emphasizing the importance of high-quality sliding back doors in the transportation industry. By conducting regular performance assessments and adhering to these benchmarks, manufacturers can enhance both operational safety and overall efficiency in their logistics processes.
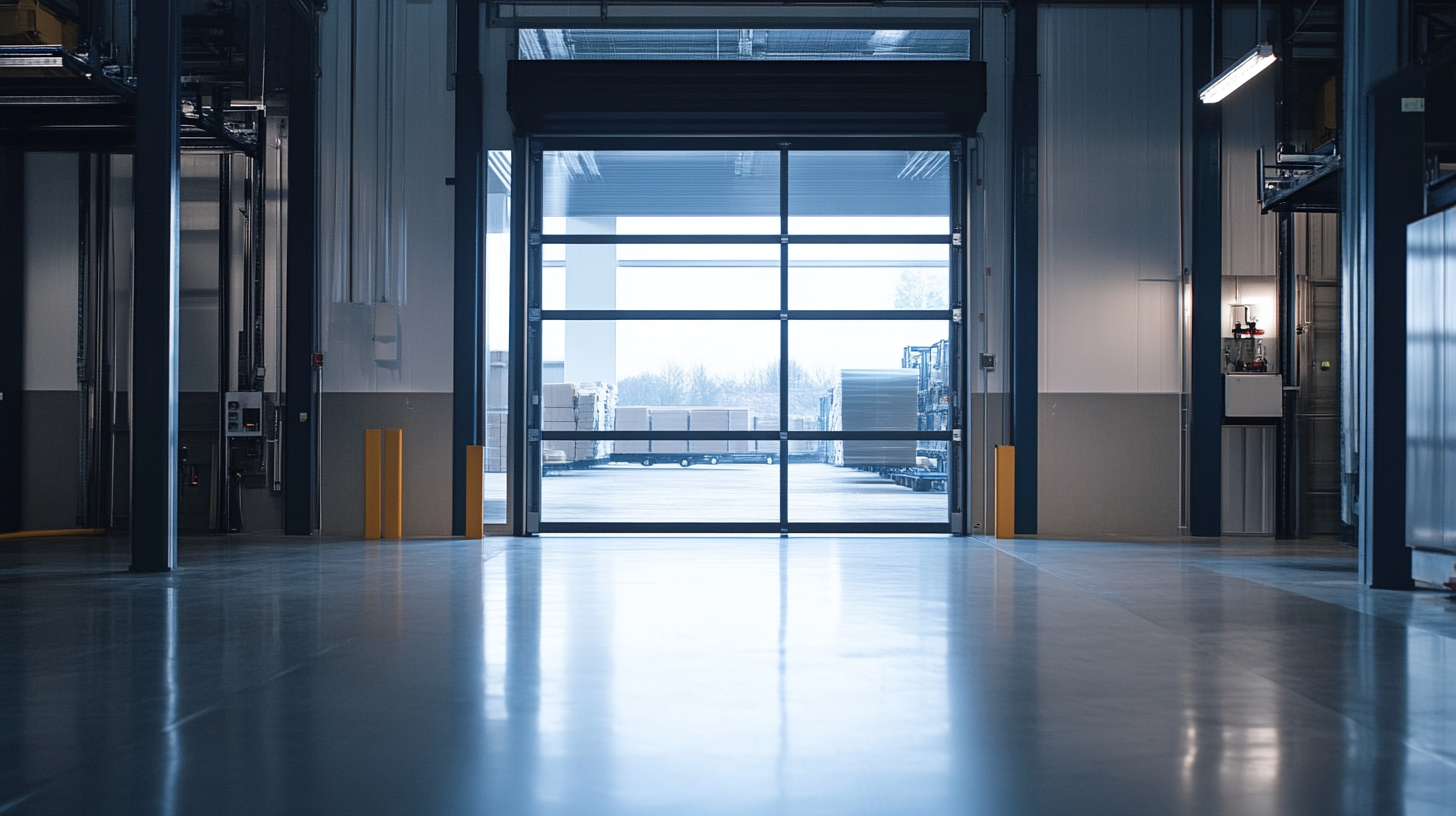
Regulatory Standards Impacting Sliding Back Door Quality
In the realm of modern manufacturing, the quality benchmarks for sliding back doors are significantly influenced by various regulatory standards. These regulations serve as critical parameters for ensuring safety, durability, and functional performance of the doors, which are commonly used in both residential and commercial settings. Compliance with standards such as the American National Standards Institute (ANSI) and the International Organization for Standardization (ISO) not only helps manufacturers meet market expectations but also enhances consumer trust in their products.
Moreover, these regulatory frameworks dictate the materials used in production, the design specifications, and the methods of testing. For instance, stringent guidelines related to impact resistance and thermal performance ensure that sliding back doors can withstand environmental stresses, thus prolonging their lifespan and maintaining energy efficiency. Manufacturers that prioritize adherence to these standards are better positioned to mitigate risks associated with product failures, ultimately fostering a culture of quality and responsibility within the manufacturing sector.
Innovative Technologies Shaping the Future of Sliding Back Door Manufacturing
The landscape of sliding back door manufacturing is increasingly being shaped by innovative technologies that cater to both functionality and aesthetics. With the rise of smart home integration, manufacturers are exploring ways to embed advanced security features and user-friendly controls into their door designs. The recent collaboration between hardware systems providers has exemplified this trend, reflecting a commitment to creating tailored solutions that enhance the overall user experience.
Moreover, resilience in the face of economic challenges is leading companies to invest strategically in innovative practices. As the industry anticipates stable sales despite a looming recession, the emphasis on resource maximization through innovation becomes paramount. Implementing cutting-edge manufacturing technologies not only streamlines production processes but also ensures that sliding back doors meet evolving consumer demands for safety and efficiency. As manufacturers continue to adapt, the role of technology will undoubtedly redefine the standards and benchmarks for quality in this segment.
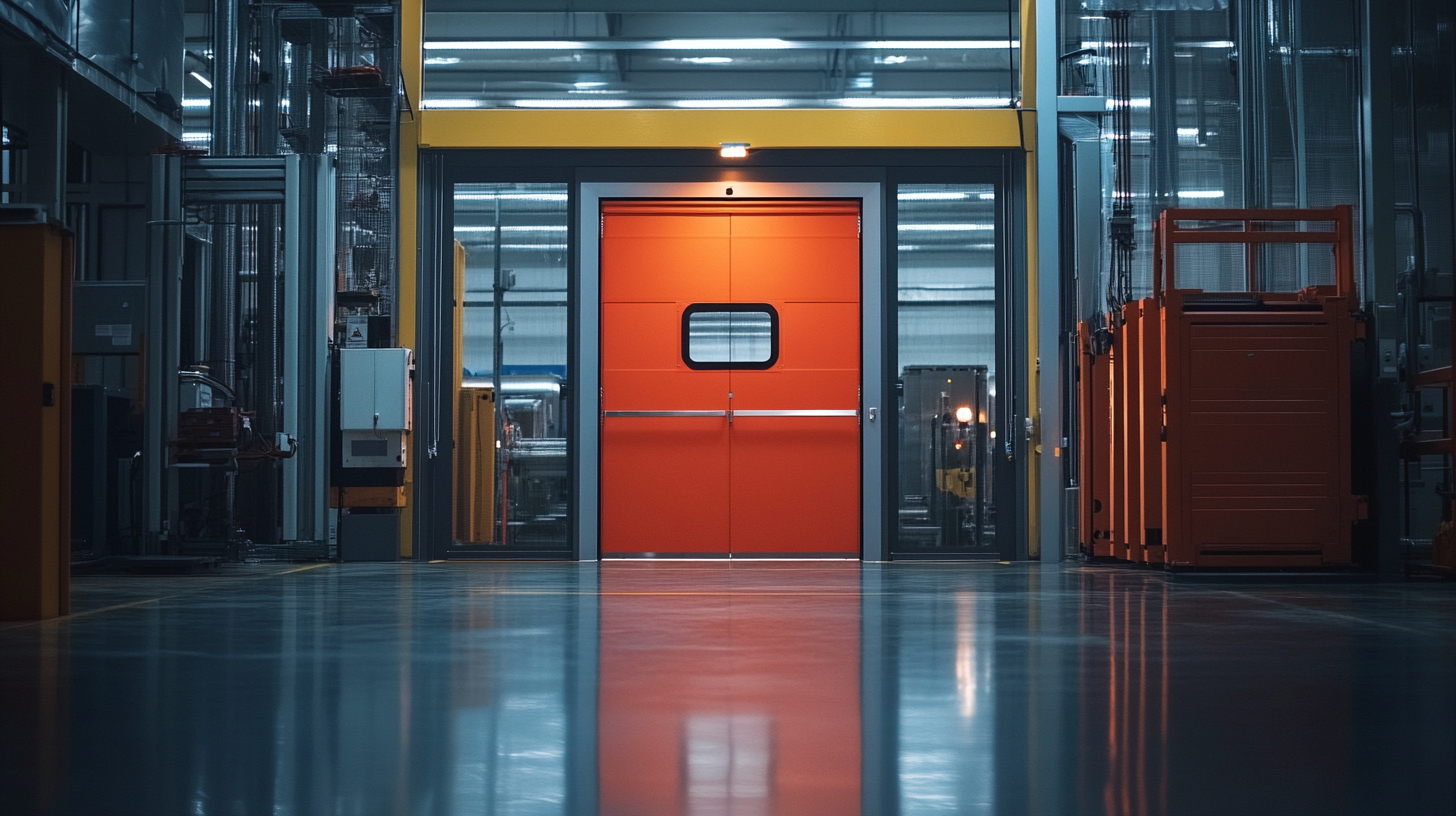